Machining of the wheel coat after reloading (Kaplan type) VILLEREST
Villerest Hydroelectric Power Station, France
Machining of the wheel coat after reloading
In June 2023, we worked on the G1 Group (Kaplan type) of the Villerest Hydroelectric Power Plant, in France, for our customer EDF.
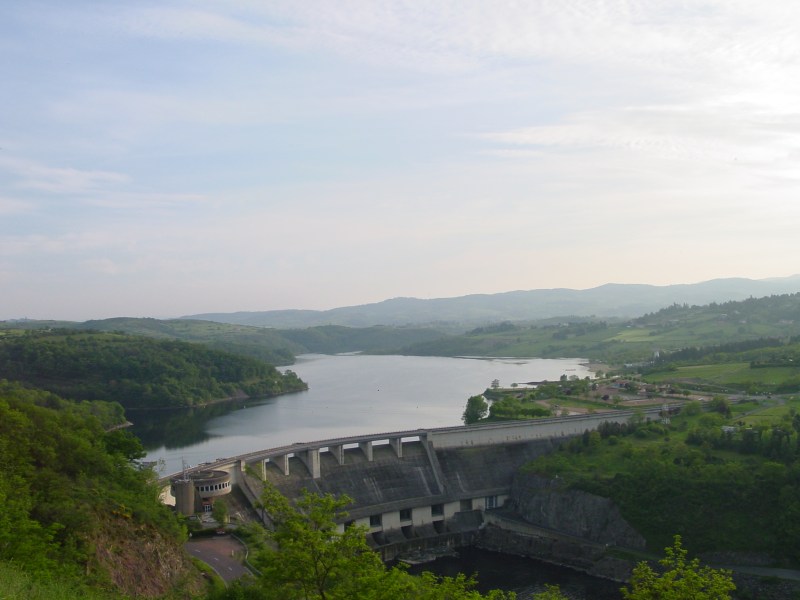
- GOAL
- TOLERANCES REQUESTED
- ACHIEVEMENT
Remanufacture the cylindrical and spherical part of the existing wheel mantle after reloading to return to the original shape and ribs. The portion to be taken back extended over a height of about 1000mm.
- Final side of cylinder and sphere: Ø3400mm
- Surface Condition: Ra 3.2
Our intervention took place in several stages:
- Step 1: Analysis of the subject in our Design Office (feasibility, 3D modeling of the turbine, study and calculations to determine the profile of our shape copying element, implementation of our machine in the 3D work environment).
- Step 2: Carrying out pre-work checks (Laser Tracker) by an external company.
- Step 3: Installation of our machine on site and machining.
- Step 4: Realization of after-work checks (Laser Tracker) by an external company.
The intervention is identical to that of the Fessenheim wheel mantle, but on a smaller diameter. A smaller machine was therefore used for this operation.