Rehabilitation of group G4 (Francis type) πππππ
Rehabilitation of Group G4 (Francis type)
In mid-2023, we worked on the G4 Group (Francis type) of the Revin Hydroelectric Power Plant in France for our customer EDF.
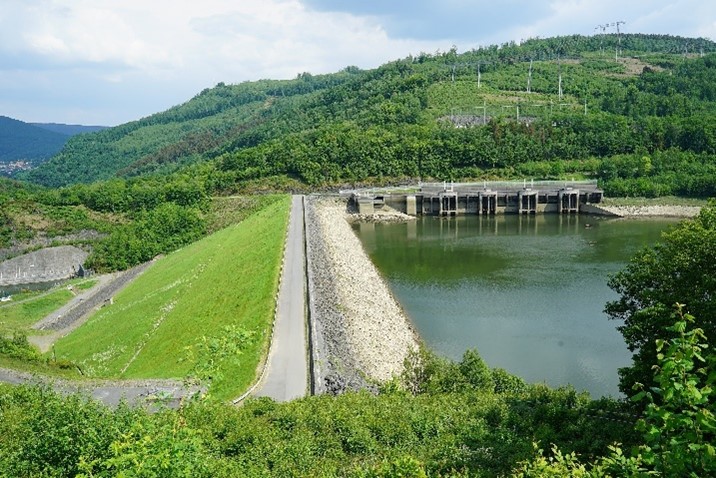
- GOAL
- TOLERANCES REQUESTED
- ACHIEVEMENT
- Recovery of different turbine elements
- Return of the scope Γ2820 H7 on the wear part and change to diameter Γ2816 H7 after reloading
- Return of the scope Γ2875 H7 on the wear part side and change to diameter Γ2872 H7 after reloading
- Surface straightening perpendicular to span Γ2875 (1 to 3mm)
- Counter-drilling and tapping of 12 M16 holes for fixing the wear part
- Cylindricity of diameters Γ2816 and Γ2872: 0.4 mm
- Coaxiality / Concentricity of diameters Γ2816 and Γ2872: 0.4 mm
- Perpendicularity of upright surface to diameter: 0.2 mm
- Straightened surface flatness: 0.3 mm
- Depth of drilling / tapping: 0.5 mm
- Surface condition: Ra 1.6 minimum
- Β
Our intervention took place in several stages:
- Step 1: Analysis of the subject in our Design Office (feasibility, 3D modeling of the turbine and the wear part, implementation of our machines in the 3D work environment for the different operations).
- Step 2: Carrying out pre-work checks (Laser Tracker) by an external company.
- Step 3: Installation of our machines on site and machining.
- Step 4: Realization of after-work checks (Laser Tracker) by an external company.